In the construction and building sector, water damage is a frequent issue that can lead to serious complications if not managed effectively. Milliken Formwork FWK169, a well-regarded product in this field, is not exempt from these challenges. To ensure the durability and reliability of your construction projects, it’s essential to grasp the specifics of how water damage affects Milliken Formwork FWK169.
This guide provides a detailed examination of the causes, detection methods, preventative measures, and repair strategies for water damage related to Milliken Formwork FWK169. By following these insights, you can safeguard the quality and longevity of your construction endeavors.
Common Causes Of Water Damage In Milliken Formwork FWK169
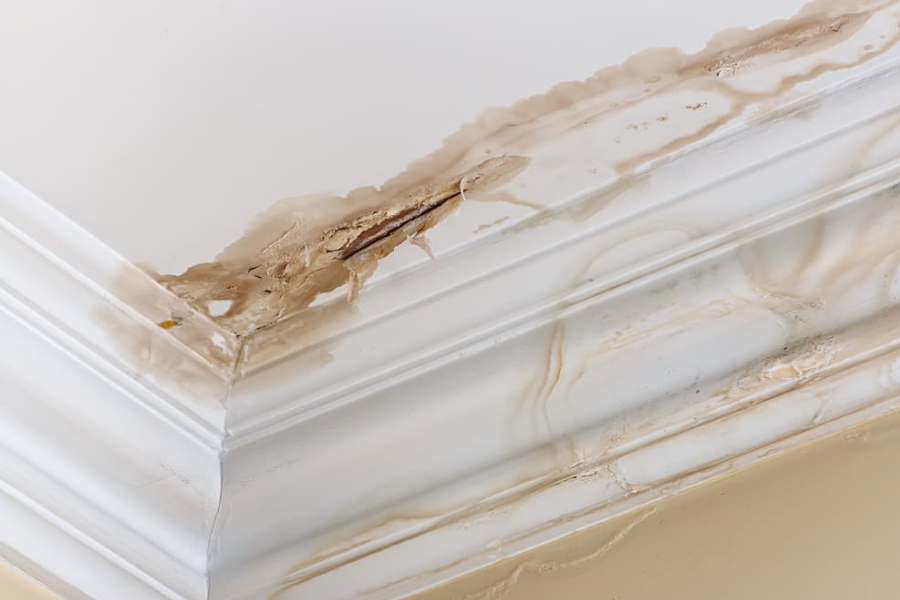
Water damage in Milliken Formwork FWK169 can stem from several key factors. One major cause is sustained exposure to moisture, which may arise from heavy rainfall, flooding, or elevated humidity. Ineffective drainage around the construction site can worsen this problem, leading to water accumulation and infiltration into the formwork.
Another significant factor is inadequate sealing or protective coatings. If these are not properly applied or maintained, water can penetrate and compromise the integrity of the formwork. Additionally, construction errors, such as improper installation or failure to adhere to recommended procedures, can also result in water damage.
Recognizing these common causes is crucial for taking proactive steps to prevent water damage and ensuring the lasting performance of Milliken Formwork FWK169.
Understanding Water Damage In Milliken Formwork FWK169
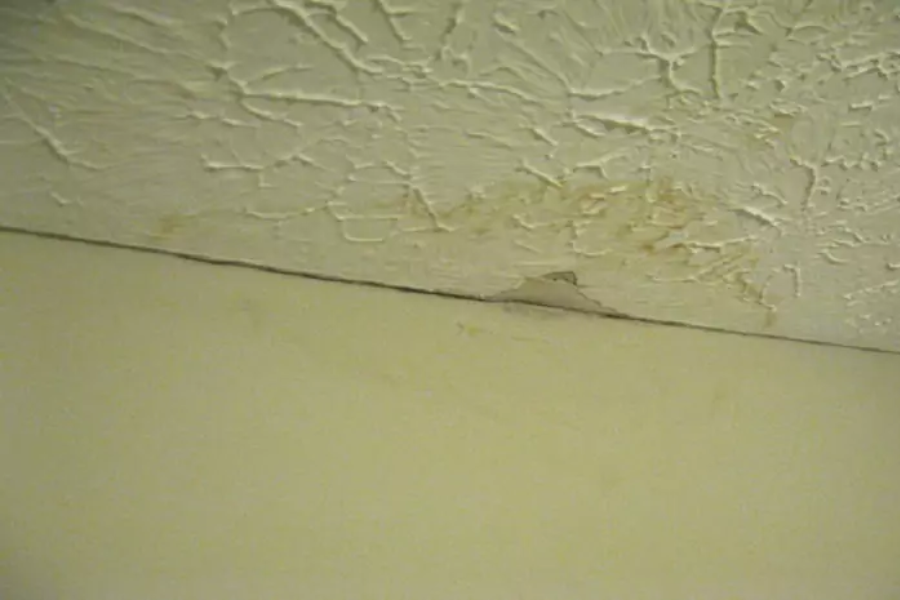
Milliken Formwork FWK169 is known for its robustness and reliability in construction. However, its structural integrity can be compromised by water damage. To effectively address and mitigate these issues, it’s essential to understand the potential causes and consequences of water damage.
Identifying Water Damage
Discoloration: Look for any unusual discoloration on the surface of the Milliken Formwork FWK169. Such changes often indicate water penetration.
Odor: A musty or damp smell can suggest the presence of mold or mildew, which often results from water exposure.
Swelling: Check for signs of swelling or warping, which may indicate that the formwork material has absorbed moisture.
Effective Strategies For Managing Water Damage
Prompt Leak Detection and Repair: Immediate action is crucial when a leak is discovered. Ensure that water does not infiltrate the Milliken Formwork FWK169 by inspecting joints and seams regularly for moisture or leaks.
Proper Drainage and Waterproofing: Maintain effective drainage systems around the formwork to direct water away from the structure. Applying waterproof sealants or membranes to vulnerable areas can also prevent water infiltration.
Swift Water Extraction and Drying: If water intrusion occurs, remove standing water promptly and initiate drying procedures to prevent further absorption. Use dehumidifiers and air movers to expedite drying and minimize the risk of mold growth and structural damage.
Mold Remediation and Prevention: Address mold or mildew growth as soon as it is detected to prevent its spread and further damage. Improve ventilation and control humidity levels to deter mold development.
Structural Repairs and Restoration: Assess the extent of any damage to the Milliken Formwork FWK169. Perform necessary repairs and replacements to restore structural integrity. Reinforce vulnerable areas and implement measures to prevent future water damage.
By understanding these aspects of water damage and following these strategies, you can ensure the continued durability and reliability of Milliken Formwork FWK169 in your construction projects.
Effective Repairs For Milliken Formwork FWK169 Water Damage
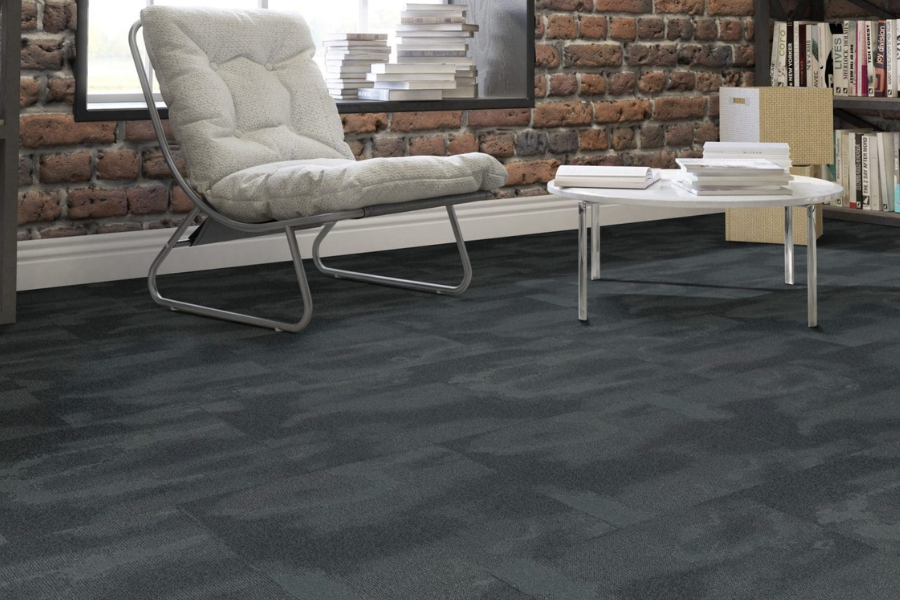
Addressing water damage in Milliken Formwork FWK169 requires prompt and effective action to prevent further deterioration. Begin by thoroughly drying the affected area to halt any ongoing water intrusion. Utilize industrial fans, dehumidifiers, and ensure adequate ventilation to expedite the drying process. Once the area is dry, evaluate the extent of the damage. For minor issues, applying a high-quality waterproof sealant or coating can restore the formwork’s integrity.
For more extensive damage, replacing the compromised sections of Milliken Formwork FWK169 may be necessary. Ensure that these repairs are carried out by professionals experienced with this specific type of formwork. Additionally, reinforce the repaired areas with protective layers to safeguard against future damage. Regular inspections of the repaired sections and prompt action on any new issues are crucial for maintaining the formwork’s durability.
Maintenance Tips To Prevent Milliken Formwork FWK169 Water Damage
To prevent water damage to Milliken Formwork FWK169, regular maintenance is crucial. Conduct frequent inspections, particularly after heavy rainfall or adverse weather, to identify early signs of water intrusion. Applying waterproof sealants and coatings periodically helps establish a strong barrier against moisture. Proper site drainage is essential to prevent water accumulation around the formwork, thus reducing the risk of damage.
Address any cracks or gaps immediately to prevent water from penetrating. Keeping the construction site clean and free from debris enhances drainage effectiveness. Using protective covers during inactive periods or adverse weather conditions can also protect the formwork from unexpected water exposure. Implementing these maintenance practices can significantly extend the life of Milliken Formwork FWK169 and maintain its optimal condition.
Case Studies: Managing Milliken Formwork FWK169 Water Damage
Several case studies provide valuable insights into effective strategies for managing Milliken Formwork FWK169 water damage. In one scenario, a construction site experienced severe water damage due to unexpected flooding. The team responded quickly by using industrial drying methods and replacing the damaged sections with new Milliken Formwork FWK169. They also enhanced the site’s drainage system to mitigate future risks.
In another instance, a building suffered water damage from prolonged exposure to high humidity. The maintenance team conducted regular inspections and applied additional waterproof coatings, effectively preventing further damage. These case studies underscore the importance of timely intervention, thorough assessment, and preventive measures in managing water damage. By drawing from these experiences, construction professionals can develop effective strategies to protect their projects and ensure the longevity of their formwork.
Preventive Strategies To Safeguard Milliken Formwork FWK169 from Water Damage
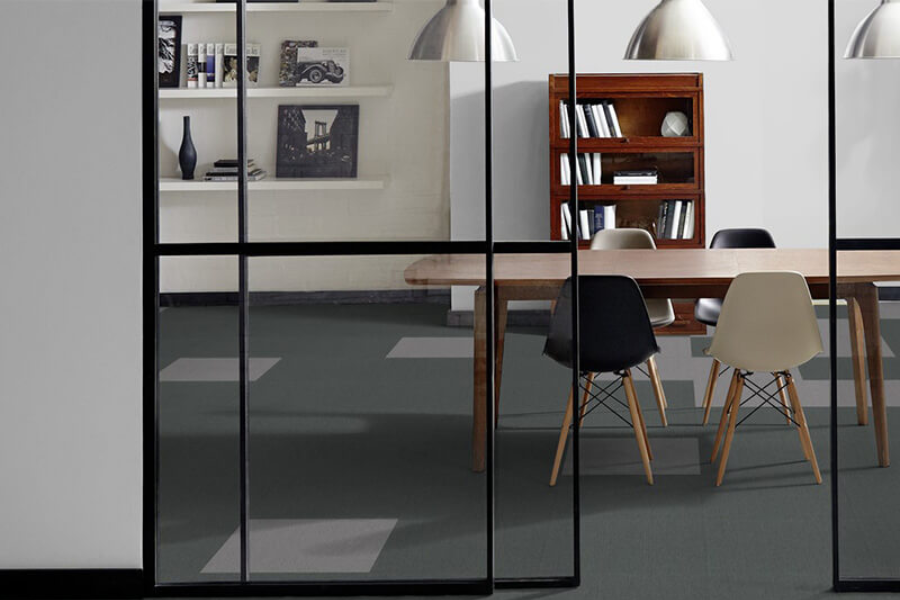
1. Thorough Sealing and Coating
Ensure that all joints and seams in Milliken Formwork FWK169 are adequately sealed with high-quality waterproof materials. Applying a robust protective coating can effectively repel moisture, thereby preserving the formwork’s structural strength and preventing water-related damage.
2. Effective Site Protection
Utilize tarps, protective covers, or temporary shelters to shield Milliken Formwork FWK169 from rain and environmental moisture. By providing proper site protection, you can significantly reduce the risk of water exposure, helping to keep the formwork in excellent condition.
3. Efficient Drainage Solutions
Install and regularly maintain an efficient drainage system around the construction site to prevent water from accumulating near the Milliken Formwork FWK169. Ensure that any blockages are promptly cleared to maintain optimal water flow and minimize potential water damage issues.
4. Routine Inspections
Perform regular inspections of the Milliken Formwork FWK169 to detect early signs of water damage. Timely identification and addressing of issues can prevent more severe damage and avoid costly repairs, contributing to the formwork’s long-term durability.
5. Management of Site Conditions
Control humidity levels and ensure proper ventilation at the construction site. Effective management of environmental conditions can reduce the risk of water damage to Milliken Formwork FWK169 by mitigating the impact of moisture and other environmental factors.
By implementing these preventive measures, you can significantly enhance the longevity and performance of Milliken Formwork FWK169, ensuring that it remains in optimal condition throughout the construction process.
Engaging Professional Services For Addressing Milliken Formwork FWK169 Water Damage
When addressing water damage in Milliken Formwork FWK169, enlisting professional services is crucial for effective remediation. Experts in this field offer a comprehensive assessment of the damage, pinpointing the exact issues and recommending targeted solutions. Their advanced drying and dehumidification techniques are essential for thoroughly removing moisture, which prevents further deterioration of the formwork. Professionals utilize high-quality repair materials and specialized coatings designed for Milliken Formwork FWK169, ensuring that repairs are both durable and compatible with the formwork.
Additionally, these services often include preventative measures, such as improving site drainage and applying protective sealants, to mitigate the risk of future water damage. By consulting with professionals, you benefit from their extensive knowledge and experience, ensuring that repairs and maintenance are executed to the highest standards and extending the lifespan of your formwork.
FAQs
1. What is Milliken Formwork FWK169?
Milliken Formwork FWK169 is a construction material used for creating concrete structures. It is known for its strength and durability, providing a reliable framework for various construction projects.
2. What are common causes of water damage to Milliken Formwork FWK169?
Common causes include prolonged exposure to moisture from heavy rainfall, flooding, high humidity, or poor drainage systems. Inadequate sealing and protective coatings can also lead to water penetration and subsequent damage.
3. How can I identify water damage in Milliken Formwork FWK169?
Signs of water damage include discoloration of the formwork surfaces, musty or damp odors, and visible swelling or warping of the material. Regular inspections can help catch these issues early.
4. What are some effective strategies for mitigating water damage?
Effective strategies include prompt leak detection and repair, proper site drainage and waterproofing, swift water extraction and drying, mold remediation, and regular structural inspections.
5. What should I do if Milliken Formwork FWK169 shows signs of water damage?
First, dry the affected area thoroughly using industrial fans and dehumidifiers. Assess the damage to determine if repairs or replacements are needed. Apply waterproof sealants or coatings to restore integrity and reinforce vulnerable areas to prevent future damage.
6. How can I prevent water damage to Milliken Formwork FWK169?
Preventive measures include applying high-quality waterproof sealants, using tarps or covers for site protection, maintaining efficient drainage systems, conducting regular inspections, and managing site conditions such as humidity and ventilation.
7. When should I consult professional services for Milliken Formwork FWK169 water damage?
Consult professionals if the damage is extensive or if you are unsure how to assess and repair the damage. Professionals have the expertise to provide accurate assessments, advanced drying techniques, and specialized repair materials.
Conclusion
Water damage to Milliken Formwork FWK169 can pose significant challenges to construction projects, potentially compromising the formwork’s structural integrity and longevity. Understanding the common causes of water damage, recognizing early signs, and implementing effective mitigation and preventive strategies are crucial for maintaining the formwork’s durability. Promptly addressing any water damage with proper repair techniques, and seeking professional assistance when needed, ensures that the formwork remains in optimal condition and continues to support the structural integrity of your construction projects. By following these guidelines and maintaining vigilant oversight, you can safeguard your formwork against water damage and extend its service life.